Teamcenter Quality software supports a closed-loop quality approach from design to manufacturing. Built on top of the Teamcenter software product lifecycle management (PLM) backbone, Teamcenter Quality helps you leverage product and process information, as well as share cross-departmental workflows so you can streamline the core quality management processes.
Teamcenter Quality works in the Active Workspace client (AWC) for Teamcenter. Active Workspace is an innovative web-based client platform that simplifies PLM for all users involved in product lifecycle, accelerating user adoption and shortening time-to-value by providing an intuitive experience anytime, anywhere, on any device.
Let’s find out detailed information with Vietbay below!!!
Key new features
Teamcenter Quality version 2312 incorporates several improved application capabilities and features.
Keep all relevant data in the QM workspace
Starting from version 6.1, using Teamcenter Quality enables you to work in a quality management (QM) workspace. The QM workspace has been further extended and improved. After opening the application, a preconfigured view appears, which can be adapted by the service at any time. As an additional improvement, Active Workspace has a new tile for each module.
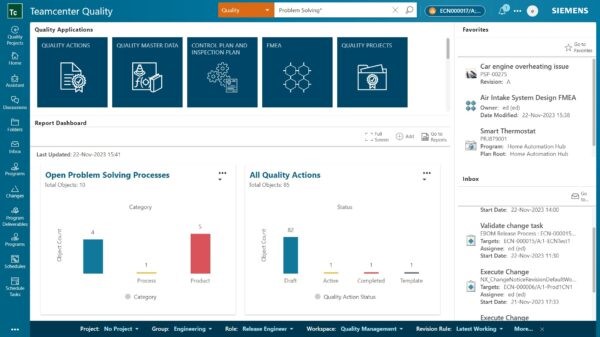
Enhancing quality capabilities for Q-gates and checklists
The focus in the current version is to assess the questions and the entire checklist with enhanced quality master data and functionalities for quality checklists. The checklists have been extended for use in quality project management, especially for mapping the supplier production part approval process (PPAP). In the Quality Project Management module, if an activity is associated with the delivery of one or more documents, it can be directly attached to the question/task on the overview page. Using Teamcenter Quality now allows you to streamline more of these tasks with improved capabilities to track quality projects such as advanced product quality planning (APQP) or supplier PPAP projects.
Improved FMEA tools and linkages provide quality deliverables
The Teamcenter Quality FMEA module helps you avoid defects by allowing you to evaluate the effects caused by potential problems early in the planning phase. The Teamcenter Quality FMEA version 2312 provides an essential piece of the puzzle to fully support the methodology, which is related to introducing special characteristics, and can be defined for failure representations inside FMEAs. You can already derive a control plan from the process FMEA. Now if a control plan was created with improved visibility for control plan linkages, the user can see it in the FMEA. Displaying the control plans derived from the respective FMEA continues to improve closed loop quality. Implementing the risk matrix in the last version was already a valuable addition. Now the risk matrix is enhanced with the risk matrix results (RMR).
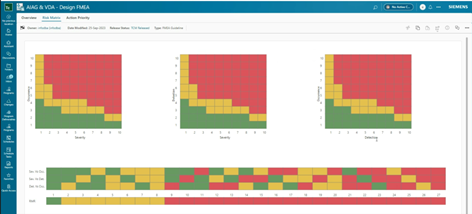
Optimize planning quality inspections
You can use Teamcenter Quality Control and Inspection Planning to improve product quality while decreasing development time. In the latest version, enhancing naming rules are available for the quality master data. A new attribute – decimal places – has been introduced for variable characteristics based on the number of decimal places for nominal value and tolerances that are shown. The support the automatic ballooning of characteristic-relevant information has been improved, especially with the model views defined in the 3D model. Beyond the enhanced ballooning functionality, other enhancements for better usability are available. Multiple references can be added inside the inspection definition or on the control plan level. Another important element is the possibility of copying the control plan structure, a new duplicate function offers the possibility of copying the complete control and inspection plan structure.
Realizing smoother problem-solving process
The Teamcenter Quality Problem Solving module comes with additional updates in version 2312 to include valuable enrichments such as in root cause analysis (RCA). Another improvement is related to quality checklist functionalities that impacts the root cause analysis. Many new functionalities are provided in the checklists, that includes checklists for problem-solving process (PSP), too. One of the most beneficial features of this latest version is the definition and key performance indicators (KPIs) in standard reports for overall PSPs.
Improved quality actions management functionalities
Using Teamcenter Quality offers quality action management (QAM) capabilities for creating and performing actions in the context of several Teamcenter Quality modules or as a standalone action. In the QAM, it is now possible to add new supplementary proprieties to each action, such as graphic symbols to highlight the action status.
Benefits of our quality management solution
- Efficiently manage the quality checklists for better assessment
- Simplify tasks on quality project management best practices to manage quality and project milestones
- Deliver enhanced FMEA tool
- Optimize planning quality inspection leveraging drawings and models
- Provide greater defect descriptions to facilitate problem solving
- Close the loop in your root cause analysis with a deeper evaluation
Learn more:
- What’s new in Teamcenter 2312?
- Teamcenter and Microsoft Teams – driving industrial productivity with generative AI
- Teamcenter X – Top 6 use Product lifecycle management software in the Cloud
Source: Siemens
Vietbay is proud to be a close partner of Siemens in providing enterprise software solutions. We always update the software with the latest and most optimal features for customers. With more than 20 years of development in this field, we are committed to bringing the best value to customers. Coming to Vietbay you will receive: “Best solution – Best service – Optimal cost“
Contact us for free and detailed advice