With the motto of constantly improving training quality, meeting the need to provide high-quality labor resources in accordance with the 4.0 technology trend for businesses, in 2021, Hanoi University of Industry has invested in the Smart Manufacturing Factory Research Center. This project is with the participation in implementation, configuration, installation and technological transfer of Vietbay Company and the support from industrial software company Siemens DISW.
The Smart Manufacturing Factory Research Center has the function of researching and developing science and technology topics and conducting training courses to provide high-quality human resources to meet the needs of labor markets. This system of research and practice rooms includes a full range of solutions from product design and development, mold manufacturing, 3D printing support design, factory digitization, planning to control production operations, automation connection and cloud computing data collection (IoT). They are in accordance with the technology trend of Industry 4.0. Currently, the center is divided into 5 specialized research rooms corresponding to the stages of the production chain of the smart factory:
Room 1: Product development design
This room includes a computer system, an internal network connection system, the integrated installation of copyrighted industrial software on product design, simulation, analysis, and optimization of product design, the use of measuring equipment for vibration and noise testing, product lifecycle management (PLM) software integration for data management, BOM management, process management, and planning management.
Room 2: Mold and 3D printing
The computer system connects to the internal network and installs and integrates software for designing molds, stamping molds, continuous molds, electrode design, simulating the plastic injection process, and simulating single-step stamping. Besides, there are some programs, such as CAM machining programming for CNC milling machines from 2.5 to 5 axes, CNC lathe machining programming, combined milling and turning programming, wire cutting machining programming, cycle management software integration product lifecycle (PLM) for data management, BOM Management, process management, and planning management.
Room 3: Factory Digitization
The computer system connected to the internal network is installed with integrated copyright software with the function of performing factory reconciliation, including:
Simulate the operating process of a manufacturing plant.
Simulate production lines with components such as robots and people;
Provides planning tools, production planning and execution management, product lifecycle management (PLM), and application software lifecycle management (ALM) tools.
Room 4: Basic Drive and Automation
This room has programming toolkits, SCADA interface design, connection, and data transfer to cloud computing. Equipped with basic PLC automation hardware and software, the HMI/SCADA production management and monitoring system allows programming, installation, management, and monitoring of all operating statuses and information. number of devices.
Room 5: Automation and process control
Programming toolkits for complex process control systems require high safety, have a distributed control system, and simulate the entire control process of the system, production, and assembly line.
This room is equipped with modern, advanced automation equipment with high redundancy mechanisms and in-depth advanced programming, used in practice for large production systems for industrial plants and manufacturing plants as well as mechanical assembly…
Connection between rooms in the smart factory research center
The center, with five functional rooms, not only operates independently but can also connect with each other. Therefore, enhancing the application of the research center for many purposes in research and training related to academics at the university.
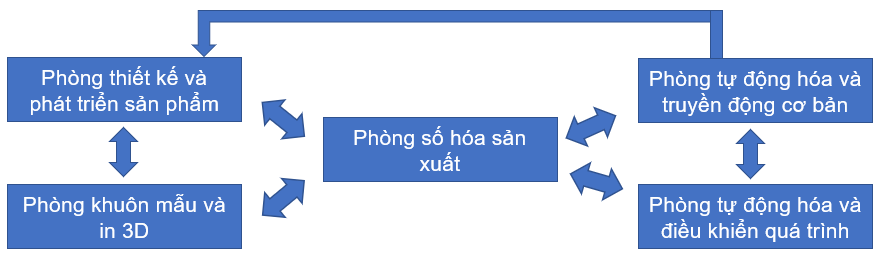
#vietbay #haui #smartfactory #siemens