The trend of digitalization has been affecting global production, businesses are looking for solutions that can comprehensively digitize all stages of the design, production, and product launch process to serve their purposes. The goal is to improve quality, increase productivity, and shorten time, thereby increasing global competitiveness. For the field of designing and manufacturing industrial machines and automation machines, the requirements are increasingly diverse and more stringent, such as: fast time to market, high level of complexity, flexibility. and personalization, energy saving, smart integration and compatibility with other systems, in addition, the needs of IoT connectivity, remote monitoring or even remote maintenance have also been considered. implementation mind…
To meet the above trends and requirements, businesses must constantly improve and apply new technology. One of the current solutions that industrial and automation machine manufacturing businesses are pursuing is to build a digital twin that works before and in parallel with the physical product combined with virtual reality technology (VR), augmented reality (AR), 3D printing technology, enhancing interdisciplinary collaboration between mechanics, electricity, electronic and automation at the same time during the same design time. The solution below will more clearly describe the solution to building digital twins of industrial and automation machines
Requirements management
First, starting from the overall requirements and product technical requirements, these requirements will be defined in detail and will be aguideline throughout the design process. The solution provides a product lifecycle management (PLM) platform that allows you to effectively manage requirements and link them to each machine component to ensure that requirements are always met and that requirements are met. This request will also be automatically linked and retrieved to the relevant department. In addition, any arising requirements and changes to requirements are automatically updated and communicated to relevant parties through the requirements management system.
Concept design and evaluatation
Based on the initial requirements, technical teams proceed to develop initial design ideas and combine simulation tools to evaluate the behavior and operating scenarios of design ideas, then choose the most optimal design idea. This initial design concept development process also combines the participation of mechanical, electrical and automation teams to evaluate ideas. NX MCD and NX animation designer solutions enable users to easily capture, model design ideas and simulate operational scenarios to validate ideas with a visual environment, enabling cross-industry integration. mechatronics and automation. Initial idea scenarios can also be used to discuss with customers if the business is a supplier of machinery or JIG to its customers. In addition, the business can combine use with VR/ AR to enhance product experience.
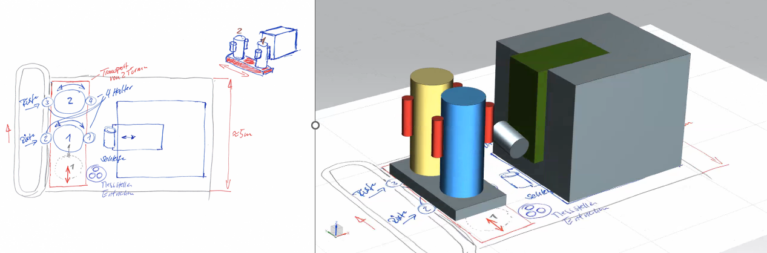
Collaboration design
After agreeing and selecting the initial design idea, the technical teams (MCAD, ECAD, Automation, Software) will conduct detailed design to complete the machine structure including mechanical components and systems. Drive systems, electrical components, electronic components, automation control components… at this stage, technical teams will work together in parallel on the same product lifecycle management (PLM) platform. ), all interactive processes and design changes are communicated to relevant departments immediately on the system. This helps the design and development process faster, increases the efficiency of searching and reusing data, and uses the correct version of the data. The design approval process is also done on a digital platform, making it easy to access in real time.
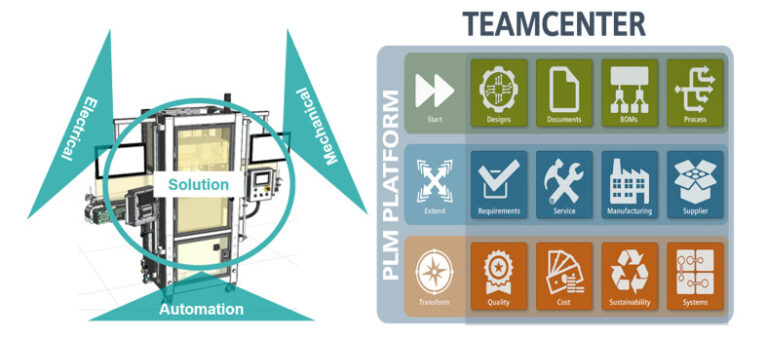
Simulation and optimization
To evaluate and optimize machine performance, the machine structure will be simulated for analysis and optimization, and promptly adjusted right from the design stage in the virtual environment before experimental production. This makes design and development faster, reducing the time and cost of actual testing. Simulation problems with diverse objectives include assessment of structural dynamics, vibration analysis, structural durability and stability calculations, heat and flow calculations… Simcenter’s Simcenter simulation solution Siemens provides comprehensive functionality to simulate and analyze all of the above problems, and a special feature is that the solution is seamlessly integrated with MCAD and ECAD design tools to minimize data pre-processing time. when simulating.
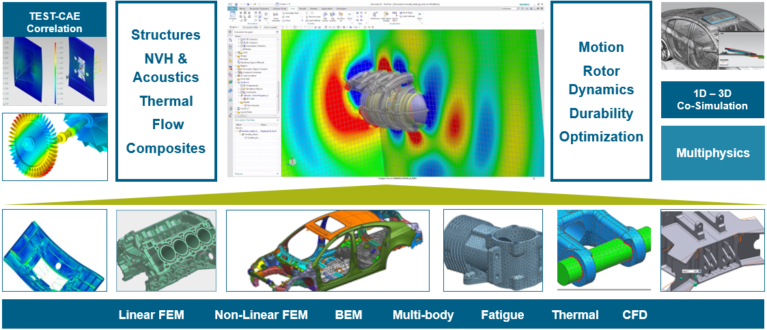
Virtual commissioning
In addition, the solution also allows connection to virtual PLC controllers or real PLCs to virtually operate operating scenarios on the machine’s virtual environment, users can also simulate control screens or control switches. The machine’s controller then performs control through PLC programs like controlling a physical machine. This helps the industry validation process to be carried out right in the virtual environment, the automation team will participate earlier in the machine design and development process, this is also the basis for evaluation and optimization. Machine operating scenarios for both mechanical and automation parts
IIoT connection
Machines can be connected to IIoT to collect and analyze data during real-time operation to provide performance assessments, failure predictions, and more. maintenance… Siemens provides a comprehensive platform for connecting, collecting and analyzing data
Enterprises manufacturing industrial machines and automation machines can also expand the use of intelligent design optimization tools (generative design), 3D printing support design (complex structural components). complexity, minimizing weight), combining simulation and virtual reality to review and evaluate machine operations with a more intuitive feel.
With the ability to integrate synchronously on the same software platform, it allows design teams such as the mechanical team, electrical automation team, and electronics team to participate at the same time and interact. to offer the most optimal product while saving time on product design and development.
The solution also integrates software for data management, documents, processes, material list BOM, change process management, requirements management, supply chain management… on a single, integrated platform. Teamwork to minimize errors, increase reuse, and enhance work interaction on digital platforms. Processes and documents are standardized and digitized
The special and optimal point of the solution is the synchronous integration on a single platform, allowing to reduce data conversion time, data version errors, and increase reuse and work interaction. team, easy data management, change management, request management.
Vietbay has 20 years of professional operation in the field of consulting and technology transfer of IT software and technology solutions for optimal design, processing, simulation, analysis, evaluation and life cycle management solutions. products (CAD-CAM-CAE-PLM). Vietbay is the first Distributor and Gold Partner of Siemens Industries Software in Vietnam, the main Partner of Autodesk, Vericut , CIMCO, WorkNC… Especially VTC – Vietbay Training Center is an Authorized Partner of Siemens Industries The software trains according to the company’s standard curriculum and issues certificates according to international standards from Siemens or prestigious certifications from Vietbay throughout Vietnam.
Contact Vietbay for direct advice on smart manufacturing technology solutions , comprehensive factory digitization, integration and synchronization in accordance with the 4.0 Industrial Revolution trend in the electronic and automotive components industries . motorbikes, molds, consumer goods, industrial machines…