PCB design is the entire process of creating a Printed Circuit Board (PCB) through collaboration and integration between multiple disciplines and multiple domains which includes electrical, mechanical, software, system, test, and manufacturing. It’s a team effort that requires constant bi-directional communication.
With the recent COVID-19 pandemic negatively affecting all industries regarding supply chain vulnerabilities, achieving success in PCB design now also includes enabling supply chain resilience for electronic systems design. This incorporates implementing an outside-in approach with supply-chain intelligence by shifting left best-known part availability, BOM validation, and validation of alternates at point of design. Having the knowledge, intelligence, and optimization at the point of design is key to achieving success for design for resilience when it comes to PCB design.
The state of design in electronics today is at its most complex and intense as ever before. Design teams must deliver more complex products on even more compressed schedules, but they lose valuable time with unproductive tasks. Connect them through all engineering disciplines and give them best-in-class solutions to thrive with a collaborative approach to electronic systems design.
PCB design: a cityscape
One of the simplest explanations or metaphors for PCB design that I really like, is that it’s like “designing a city.” A city containing land (real estate), structure foundations, buildings, houses and roads all connecting to each other. The land (real estate) and structure foundations of a city represent the stack-up of the PCB. The building and houses represent the electrical and mechanical components placed on the PCB, and the roads represent the copper traces and vias connecting everything as required.
The bare PCB is made up of land patterns for components to be attached/soldered on to the PCB. They are interconnected by a conductive printed wire referred to as a trace on a non-conductive substrate. They provide a pathway for electrical circuitry to function. This is commonly referred to as a Printed Wiring Board (PWB). It is important to note that it is not considered an assembly until all the required components are soldered on to the PWB. Once soldered to the PWB, it then makes the circuit complete. The fully assembled/populated PCB produces a fully functional ecosystem, which is where the metaphoric comparison between PCB design and designing a city is made.
Once the PCB is fully populated with all the necessary components, it is at this stage or assembly level that it is often referred to as a Printed Circuit Assembly (PCA), or Printed Wiring Board Assembly (PWBA), or Circuit Card Assembly, depending how you chose to refer to a fully populated printed circuit board.
The role of the PCB designer
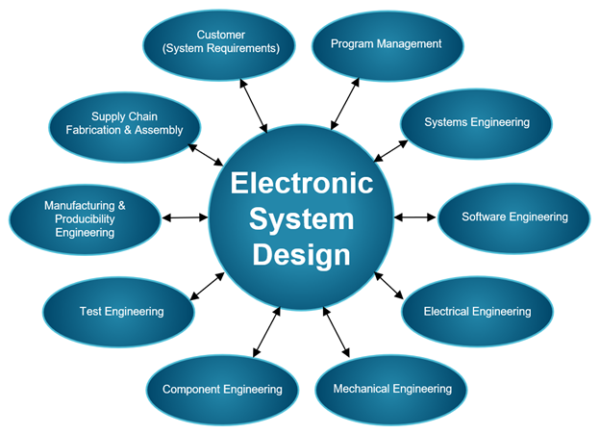
Like many engineering disciplines that tie into PCB design (electronic systems design), the PCB designer (printed circuit layout professional) plays an important role that typically sits within the electrical engineering department. Refer to Figure 1 to view the key stake holders (the departments) that typically collaborate within the overall design process in achieving project end goals, whether it be internal company goals/milestones, and or external customer requirements.
With such diverse key stake holders being both internal and external, organized complexity demands multi-discipline collaboration and integration. Refer to Figure 2 for an example of today’s system level connectivity – organizational complexity.
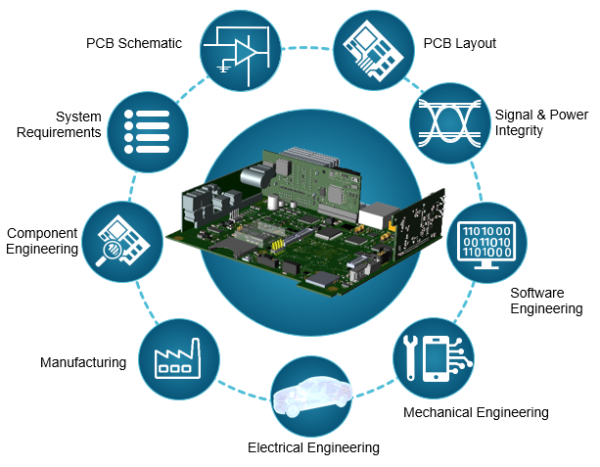
With such diverse key stake holders being both internal and external, organized complexity demands multi-discipline collaboration and integration. Refer to Figure 2 for an example of today’s system level connectivity – organizational complexity.
Typically, PCB design falls under the Hardware (HW) design category of engineering. It ties in electrical, mechanical, software, systems, test, and manufacturing disciplines to include electrical (ECAD) and mechanical (MCAD) designers.
PCB design requires many inputs and details from multiple disciplines and their respective domains to help define, validate, and produce the final product. An example of these are as follows:
1. System level requirement/architecture definition
2. Mechanical, Electrical, Software, Systems, and Test requirements/constraints
3. Signal Integrity (SI) / Electromagnetic Compatibility (EMC), Power integrity (PI) / Thermal analysis
4. Design for Manufacturing (DFM) and Producibility guidelines
5. Supply chain resilience regarding component sourcing
The hardware is typically created by mechanical definitions and constraints that feed into PCB layout along with electrical input/requirements to include schematics (graphical symbols and diagrams depicting an electronic circuit) along with electrical and physical constraints that meet the end-product definition/requirements.
PCB design has evolved from the early days of sticky back component patterns and tape placed on a mylar sheet that was then photographed to create a production tooling master artwork used for manufacturing. With the evolution in PCB design over the decades, the process, and individual roles of the key stakeholders of who does what, and when within the design process has evolved as well.
Schematics are created by an electrical or electronics engineer. The mechanical engineer provides the physical packaging or envelope with all the physical requirements and constraints. This mechanical information feeds into the PCB layout. Then, a layout specialist (electrical designer) designs the PCB layout, which is a result of a collaborated effort by multiple disciplines. This specialist has always functioned as the hub or focal point of the project team for gathering all required inputs/requirements that are to be implemented into the design of the PCB.
Printed circuit engineering: a definition
The knowledge, skill set, and experience required to be successful in PCB design has evolved into what is known today as printed circuit engineering. This evolution requires a comprehensive understanding for design of packaging solvability, performance, and manufacturing. The printed circuit layout professional/profession in today’s industry now cross pollinates the necessary skill set between electrical, mechanical, software, test, and manufacturing disciplines. You can now understand why it’s safe to say that the process of PCB design has evolved from the siloed/individual efforts to a multi-discipline, multi-domain team effort along with the profession of the printed circuit layout itself.
To help guide individuals entering or continuing in this profession, the IPC Technical Activities Executive Committee (TAEC) in 2017 accepted a recommended definition for the Printed Circuit Engineering Layout Professional that will be placed in the IPC-2200 series standards. It’s important to note that the Printed Circuit Engineering Layout Professional is only one of the significant roles within the grand scheme of PCB design. It doesn’t cover all roles in PCB design. The accepted recommended definition reads as follows and is shown pictorially
Definition for Printed Circuit Engineering Layout Professional
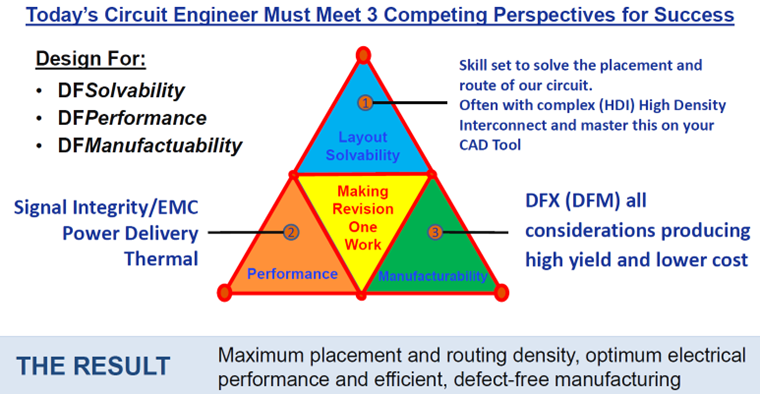
The following overview describes what are the core knowledge and competencies to best serve in the role of Printed Circuit Engineering Layout as a stand-alone professional, or as the engineer performing this responsibility. Today’s designer must address 3 perspectives for success, with the goal of making the first iteration work as intended.
– Layout Solvability – Complex Packaging Skill Set
– Performance – Signal, PWR and Thermal Performance on all Layers
– Manufacturability – DFX Considerations for High Yield and Lower Cost
The Result provides for maximum component placement/routing density achievable, optimum electrical performance and efficient, high yield, and defect free manufacturing.
PCB design best practices
Bringing all required stakeholders to the table at the initial stage of the PCB design process and by implementing industry PCB design best practices is key to overall success. Multi-discipline and multi-domain collaboration and integrations along with constant bi-direction communication between all stakeholders is vital in breaking down barriers and from working in silos. There are 5 pillars of industry PCB design best practices that are highly recommended for achieving success in PCB design. These 5 pillars are as follows:
1. Digitally integrated & optimized
2. Engineering productivity & efficiency
3. Digital prototype-driven verification
4. System-level model-based engineering
5. Supply-chain resilience
PCB design has evolved
Reflecting on the original question: “What is PCB design?”, one can see why there is so much that encompasses PCB design and why it requires more than a simple definition. PCB design has evolved into printed circuit engineering of electronic systems design. Simply put, PCB design has become a multi-discipline, multi-domain, process that requires collaboration/integration and digital transformation
Source: Siemens
For more information, please contact:
Vietbay CAD/CAM/CAE/PLM Team
Phone/Zalo/Whatsapp: 091 929 5520
Email: [email protected]
Website: www.vietbay.com.vn * www.cadcamcae.vn * www.vietbay.edu.vn