In part one, we looked at how a Digital Enterprise can use advanced engineering software to design and optimize a small electric roadster, called the SimRod. After using the Digital Twin of the SimRod to examine key performance characteristics, the vehicle was taken on a real-world driving test. Data gathered from this test suggested that a new steering knuckle design could reduce the weight of the part while maintaining its structural rigidity.
With an updated design for the SimRod’s steering knuckle, it is time to consider the production methods and technologies that will enable this part to become reality. Due to its complex, ‘organic’ geometry, the use of additive manufacturing makes sense to create the optimized steering knuckle.
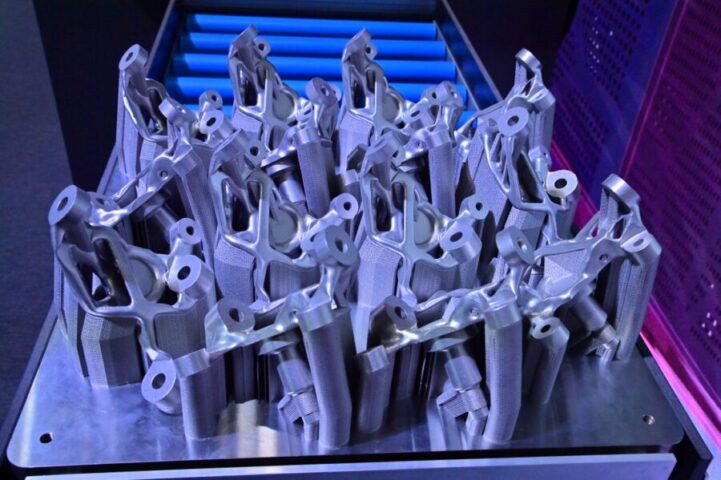
Once completed, part manufacturing technology with CAD/CAM and CNC software can be used to define the manufacturing strategy and generate the G-code for cutting away excess material and preparing the part for assembly. The manufacturing planning environment also allows production designers to check material flow throughout the facility, perform offline programming of robotic manipulators, and even design and verify processes that will be performed by humans, ensuring proper ergonomics and safety.
These capabilities can also help production facilities become more flexible and automated, allowing them to respond to dynamic market conditions quickly and increasing the scalability of the overall production system. With consideration of the rate of production, planners can identify material delivery locations and review delivery routes and corridors and simulate automated guided vehicles (AGVs) in the context of the factory layout to ensure proper functionality.
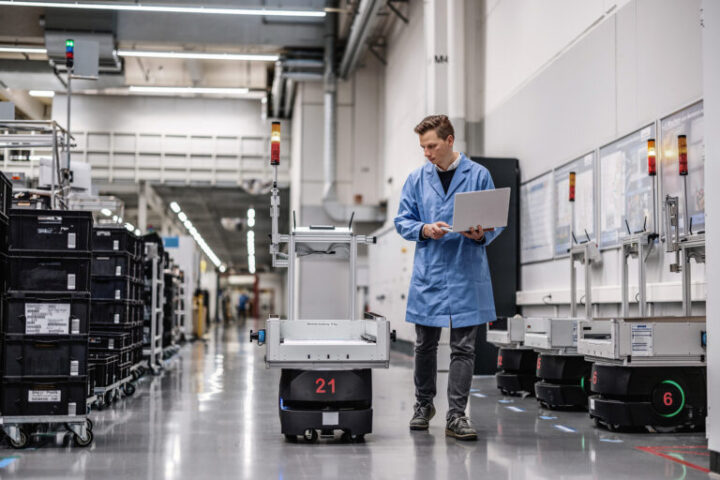
With the SimRod, we have looked at how companies that have become Digital Enterprises can design, test, improve, and produce a modern product. In addition to this horizontal story, from design to production, there are also benefits in the vertical direction, from the top floor to the shop floor.
Through the Digital Twin of the product and production, a modern Digital Enterprise can collect and synthesize data from throughout the product and production lifecycle. This leads to greater transparency, tracking capabilities, and the ability to create a closed loop of product development, production, and optimization.
Ultimately, improving communications can help capture and measure more than just product or production data, leading to the potential for a more holistic understanding of the production environment. Energy consumption, emissions, material usage, and the consumption of raw materials (such as water) can all be tracked, generating collective intelligence on the sustainability performance of a facility. Once inefficient processes are identified, they can be improved to lower the environmental impact of our production ecosystems.
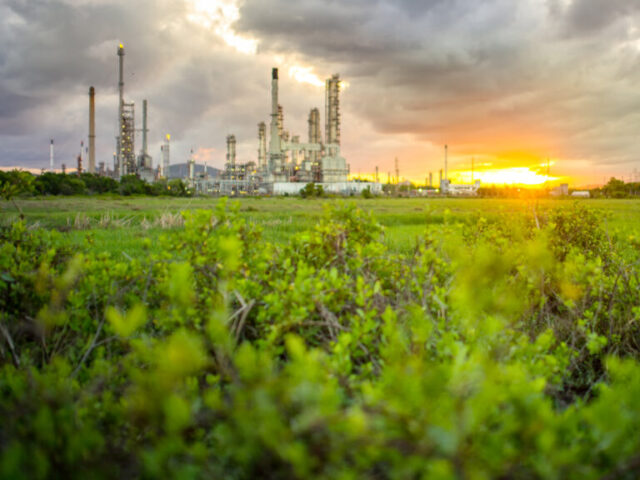
For more information, please contact:
Vietbay CAD/CAM/CAE/PLM Team
Phone/Zalo/Whatsapp: 091 929 5520
Email: [email protected]
Website: www.vietbay.com.vn * www.cadcamcae.vn * www.vietbay.edu.vn