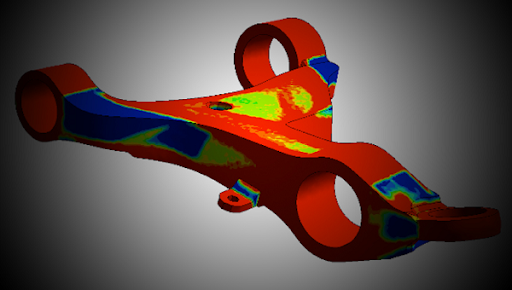
Design and Optimization of Lattice Structures for 3D Printing using Altair OptiStruct.
How would you like your burger done? Medium rare, well done, or 3D printed? Seems farfetched? Well, not so much, if the recent 3D printing trends are anything to go by. All said and done, while I am a fan of this new, potentially revolutionizing technology, I think I will stick to having my burger made the good old-fashioned way.In today’s industries, designs are usually based on the manufacturing methods prevalent, but we have seen designs intended to only be manufactured by 3D printers instead of the traditional approaches. Therefore, we can claim that a designer’s creation depends heavily on the manufacturing methods. 3D printing offers much greater flexibility in terms of manufacturability, compared to the traditional methods. However, it begs the question: are our design tools and methods in a position to take full advantage of this manufacturing flexibility? While design trends are definitely headed that way, design tools and methods must evolve quickly to support these trends in order to take full advantage of the 3D printing manufacturing capabilities. And that is where Altair OptiStruct comes in.
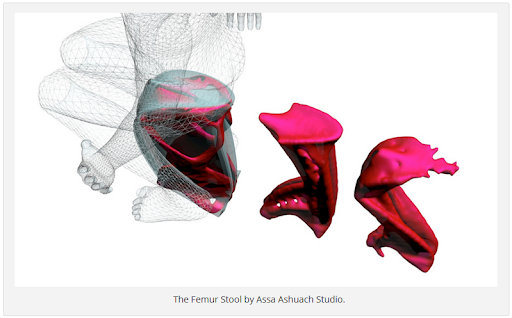
For the past 20 years, we have continued to develop cutting-edge optimization technology, particularly targeting design conceptualization where the potential for efficient, lightweight, and innovative design is maximized. One such technology is the topology optimization functionality available in Altair OptiStruct. Topology optimization reveals what the design wants to be, even before we have any CAD for it! Topology optimization is not new – for many years, Altair has evangelized and democratized this technology in a wide range of industries, and it continues to be a focus area of development.
Now, in order to obtain meaningful results from a topology optimization, the implementation was modified to suit the current conventional manufacturing techniques such as casting, extrusion, stamping, etc. Let’s take a look at the impact this approach has had on the performance of the design:
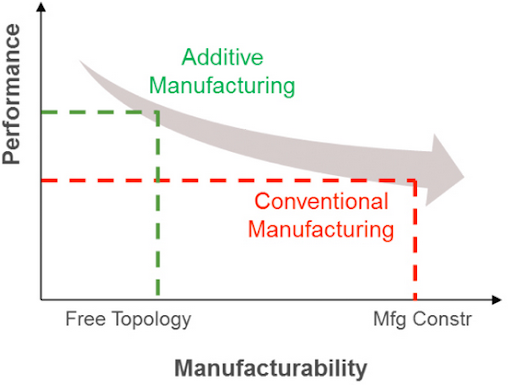
From the figure above, design performance takes a hit from the inclusion of manufacturability requirements and constraints. Unfortunately, this was the compromise to have a manufacturable design. But now, with the increased manufacturing flexibility offered by 3D printing, we can allow more freedom in topology optimization, as we are able to make a more literal interpretation of the topology results. The optimization process is not as constrained as it was traditionally, which allows us to move further up the performance curve. As a result, an inherent benefit for the same design requirement by using this topology optimization technology for 3D printed designs.
Topology optimization and 3D printing bear many similarities in their philosophies:
- 3D printing allows freedom of form. Complex designs can be easily manufactured, and designs are customized. It facilitates accelerated production since there is no need to develop for tooling.
- On the design side of the spectrum, topology optimization takes full advantage of the package space provided. It finds freeform and efficient material layouts where unique designs can be created, and the overall design process is shortened because design iterations are minimized.
These similarities provide the wonderful synergy that these two technologies share, and it is this synergy that we are capitalizing on.
Now, let’s take a closer look at a design characteristic that can only be built using 3D printing techniques – lattice structures. Lattice structures involve repetitive patterns of a particular cell shape or type. There are libraries of cell types, and the density of these cells in a design is based on the application and loading that the design experiences. A couple examples of lattice structures are displayed below.
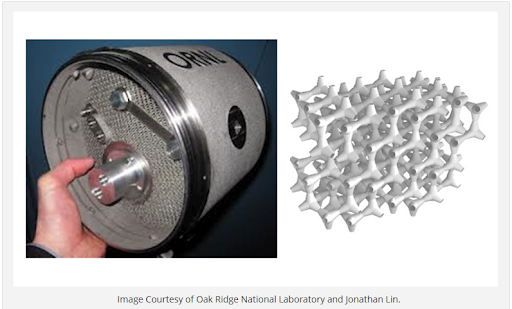
Apart from being unique to 3D printing, lattice structures bear some desirable characteristics from a design perspective. For example, due to the large network of structural members, the design exhibits better performance for stability. The large network of members also results in larger surface area, making these designs desirable for thermal behavior, such as for heat sinks. They also have desirable weight characteristics, and are used as an approach to target weight reduction. Additionally, lattice designs are great for biomedical applications, such as implants, as the porous nature of the structure facilitates bone and tissue growth and attachment.In the latest release of OptiStruct, we implemented the functionality to generate lattice structures. What is unique about this is that we don’t simply fill a volume with a lattice structure to reduce weight, but instead, we use optimization – topology optimization – to drive the material layout including the lattice regions. From this new topology optimization implementation in OptiStruct, we are able to identify void regions in the design space, where the material can be removed, regions where solid material is needed, and regions where lattice structure is required. This allows us to generate the optimal hybrid or blended solid-lattice design based on desired functionality of the part.
Lattice structures can be considered as porous structures. In the case of topology optimization, the semi-dense elements are like the porous media. With the traditional topology optimization formulation, these semi-dense elements have been penalized to produce more discrete structures like elements with either 0 or 1 as density, where 0 indicates voids and 1 indicates the existence of material. Now that 3D printing enables us to manufacture these “porous” structures, which are essentially lattice regions, we can allow the topology optimization to retain more “porosity” in the design space. In other words, the semi-dense elements are not penalized as much because we have methods to manufacture these semi-dense regions. A density range is used to identify lattice regions in order to interpret the design. Regions below the lower bound of the range are considered voids, while those above the upper bound threshold are considered solid. To aid in the overall process workflow and simplify the design engineers’ tasks, this interpretation is done automatically by OptiStruct, resulting in the generation of a complete finite element model representing the lattice structure design. The lattice regions of the model are interpreted as a network of beam elements describing a particular cell type.
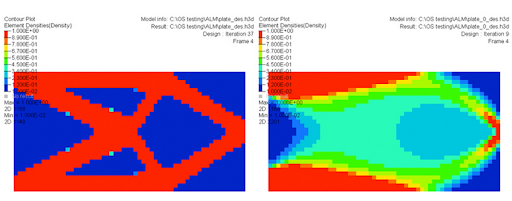
The images above showcase two topology optimization results. The one on the left uses the traditional topology penalization scheme, whereas the one on the right uses the one implemented for the generation of lattice structures. As shown, the traditional topology penalization scheme is more discrete, while the lattice structure topology optimization retains the semi-dense elements, which are then interpreted as lattice regions.
In terms of the design’s stiffness, the graph below shows how the optimization approach affects the stiffness of a design using the same mass constraint. As expected, the free topology run, without any manufacturing constraints (maximum freedom), yields the stiffest design. The lattice design, on the other hand, is stiffer than the one with traditional manufacturing constraints, which is also expected as well because the design with the traditional manufacturing constraints is penalized more.
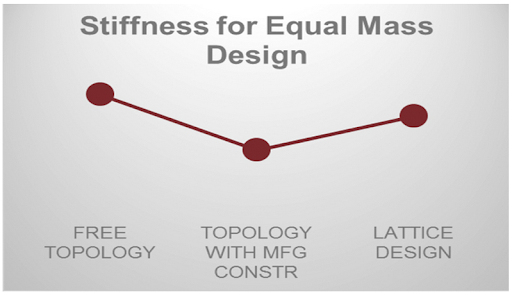
The optimization process doesn’t just stop at topology. To refine the design, in the two-phase semi-automated process that was developed (the first phase being the topology phase), the second phase involves a detailed sizing optimization where the end diameters of each lattice cell member are optimized. This allows for further weight reduction while meeting design requirements, such as buckling, stress, and displacement.
The following examples showcase the application of this process to optimize an automotive control arm designed for 3D printing by utilizing lattice structures.
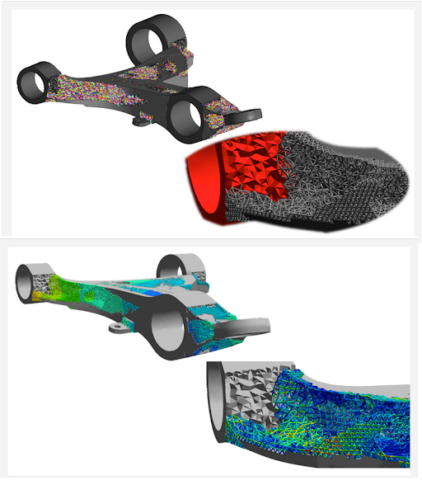
Overall, the design trends are most definitely heading towards 3D Printing with its flexibility and versatility compared to traditional methods. Without a doubt, design tools are evolving at a faster pace than ever to support a designer’s ongoing needs to create efficient, optimized, and innovative solutions. Most importantly, Altair OptiStruct is – offering endless opportunities for designers and engineers to develop the next big thing.
Views: 1,898