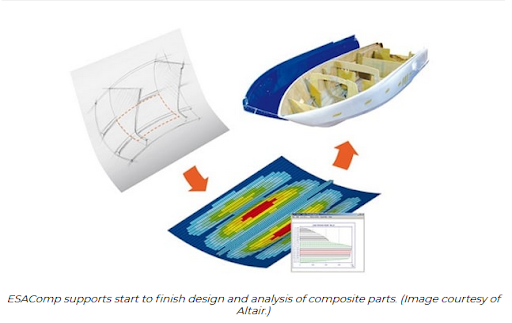
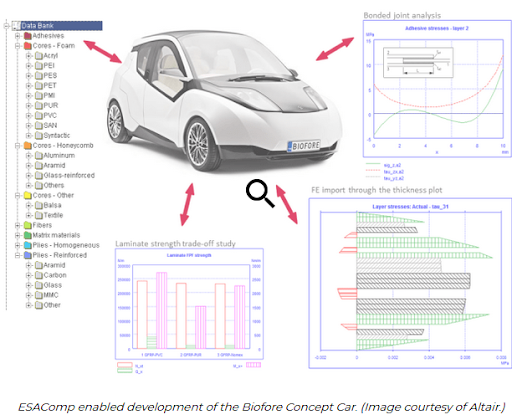
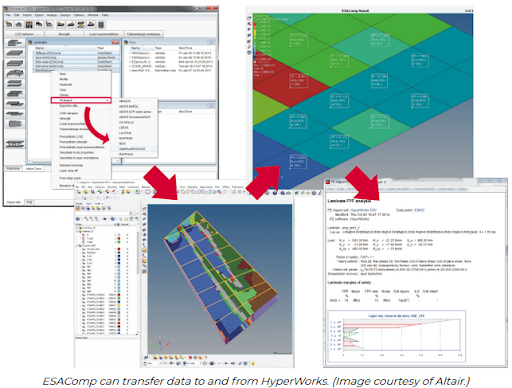
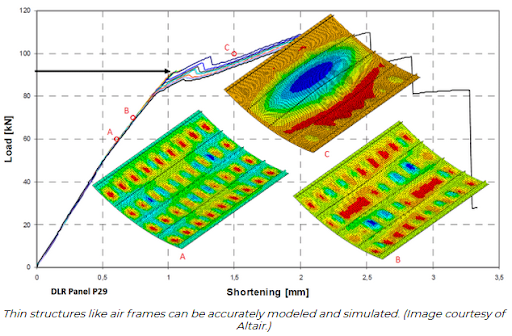
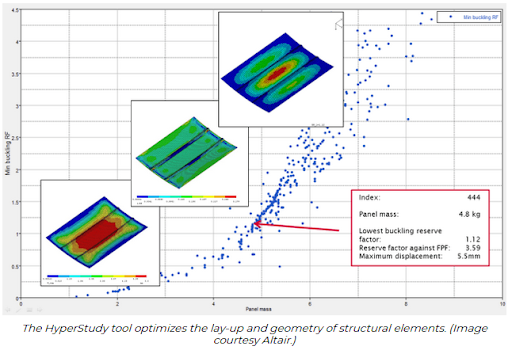
Windows Server 2022 Essentials is the Latest Server Operating System of Microsoft. This version ideal for small businesses with up to 25 users and 50 devices. When buying Essentials via OEM form, you will only receive the Key, not including the installer. No need to equip CAL when accessing the Essentials version server, 10 core […]
Window Server 2022 Standard suitable for minimally virtual or physical environments. Unlimited users and devices. The Standard version provides a license according to the number of CPU cores with the 16 core package. If more than 16 cores have to buy additional licenses for enough CPU cores. Standard edition servers can run the parent operating […]
Windows Server Datacenter 2022 is particularly suitable for modern data centers that have reached a high level of virtualization.This version contains many premium features. Virtual machine protection, which protects virtual machine firmware and startup files, and enables BitLocker disk encryption. Datacenter instance license allows unlimited number of Hyper-V virtual machines or Hyper-V containers
Windows Server 2022 User CAL stands for Client Access License, allows users to access server services legally. CAL user rights – a user can access the server software from any number of devices. This type of license is convenient in the administration of organizations where many mobile employees need to access the corporate network from […]
With Windows Server 2022 Device CAL, you purchase CALs for every device accessing your Server, regardless of the number of users using that device to access the Server. CAL equipment can make more economic and administrative sense if your company has employees using the same equipment, say, across different shifts.
SQL Windows Server 2022 Standard Edition is targeted at organizations that deploy only physical servers or use minimal virtualization environments, with only a few virtual machines. Provides basic data management for departments and small organizations to run their applications and supports popular development tools for on-premises and cloud – enabling database management efficient with minimal […]
SQL Server 2022 – 1 user CAL for Client Access License, allows users to access server services legally. Allows users to access SQL Server Standard Edition from any device, no matter how many devices the user uses. If you have multiple users that need to access SQL Server from different devices, you must purchase a […]
With SQL Server 2022 – 1 device CAL, a device can access the server from any location as long as the device has a valid Device CAL and is used by an authorized use.